Learn more about how customer success with Siemens Mobility Trains case study. Achieving time savings across maintenance activities with the help of Siemens Teamcenter solution, integrated with Cortona3D Rapid Author.
50%
Reduction in time to create maintenance manuals.
New ability to co-author maintenance manual content in tandem with engineering development.
30%
Reduction in the time spent on maintenance activity.
Siemens Mobility's Challenge:
Keep trains running at optimal levels by minimising the time that a train spends in a depot.
New trains built by Siemens Mobility began operating in the UK in early 2016. An initial fleet of 115 trains is comprised of 60 eight-car trains and 55 twelve-car trains – 1,140 vehicles in all.
Looking after these over a period of 30 years is the responsibility of Siemens Mobility, which was awarded the contract to both build and maintain the trains (see figure 1). To support this, ‘Total Service Logistics’, business model, two maintenance depots have been built as facilities where inspections on each train will be undertaken for every 20,000 miles’ usage, and significant overhauls for every one million miles’ usage.
Under the terms of this demanding performance regime, any issues with regard to the availability of trains results in a direct penalty to Siemens Mobility, so an effective maintenance protocol was central to the success of the contract. A critical requirement was therefore to keep trains running at optimal levels by minimising the time that a train spends in a depot.
Significant enablers are to ensure that up-to-date maintenance instructions are available to technicians from before product launch and in perpetuity as running changes and new engineering releases take effect; and that maintenance manuals support right-first-time repair actions by providing intuitive and easy-to-use work instructions that represent correct and viable maintenance procedures.
The Solution
Enable document creation and management as an integrated service lifecycle management solution.
The vision towards an ‘integrated service lifecycle management solution’ for Siemens Mobility meant using Teamcenter and Teamcenter CMS to integrate maintenance-manual creation and management into the digital engineering environment. In this way technical publications creation became a service lifecycle management process integrated with product development actions and processes.
The impact was to improve collaboration and teamwork between maintenance technicians and product developers or systems integrators, and to integrate maintenance-manual creation and management into engineering release workflows and processes. In this way maintenance manual information is able to always reflect the latest engineering releases and running changes.
Reduce preparation time by leveraging engineering data, including 3D CAD, for the creation of maintenance manuals
Because it drives documentation creation from source CAD data, used in conjunction with Teamcenter, Cortona3D RapidAuthor allowed the fast introduction of preset animation actions allowing a part’s assembly or disassembly to be quickly animated. At Siemens Mobility, an author creating a disassembly-to-assembly process can now also clone the process and invert it to rapidly create a fundamental install process, or vice versa.
When the procedure authoring is complete, Siemens Mobility can also generate a document which re-uses the procedure to position critical step information automatically (such as parts numbers and action descriptions). On completion of the content authoring, illustrations may be added and the document can then be published and automatically formatted using a pre-created stylesheet.
Reduce delays and improve right-first-time by facilitating the delivery of work instructions in an interactive, visual format
The new Teamcenter-based solution means that publications information is easy to keep up to date: when an update is required, associativity to the source CAD data allows easy notification to authors and fast update in a semi-automatic fashion.
Siemens Mobility’s use of Teamcenter CMS means that any document is configured by the software from modular elements, and thus represents the specific configuration of the assembly needed by the maintenance technician for the product variant he or she is working with.
And today at Siemens Mobility the interactive nature of the published output ensures the content reflects reality as closely as possible; replacing the need to use complex and lengthy descriptions of processes (which are easily misinterpreted) with clearer, concise interactive animations that directly demonstrate the process.
The Impact
Authoring/ content-creation impacts.
From a document-authoring perspective, the impact of adopting Teamcenter CMS and Cortona3D RapidAuthor at Siemens Mobility has been able to reduce the project time to create maintenance manuals by 50%. Where creating an individual work instruction previously took days, Siemens Mobility authors can now fulfil this task in 6-to-10 hours.
The impact of this 50% reduction in time required to create maintenance manuals, together with the parallel capability to co-author maintenance manual content in tandem with engineering development, has proved to be a dramatic enhancement to Siemens Mobility’s business – enabling maintenance-manual readiness to be achieved 6 months ahead of product launch.
Downstream impacts
Siemens Mobility maintenance technicians now able to access 3D interactive work instructions on ruggedised Windows tablets. Early delivery of content facilitated the identification and resolution of maintenance issues ahead of product launch, averting delays and inefficiencies typically experienced in rail fleet maintenance contexts.
As Siemens Mobility have moved into implementation in early 2016, the post-product-launch benefits of the Teamcenter solution are also becoming readily apparent. Technicians can be sure of having the exact content for the configuration of car that they are working on at any given time, and as 3D interactive data, have a class-leading, intuitive and comprehensive set of instructions to work from. From all this, Siemens Mobility are experiencing a 30 percent reduction in the time spent on maintenance activity.
Proud to be working with
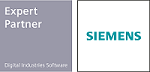
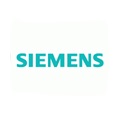
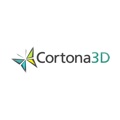
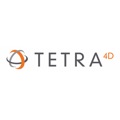
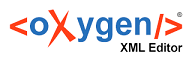