Offering a range of digitalised Technical Content solutions to aid in the creation and maintenance of effective product documentation for complex equipment, from maintenance manuals to work instructions and more.
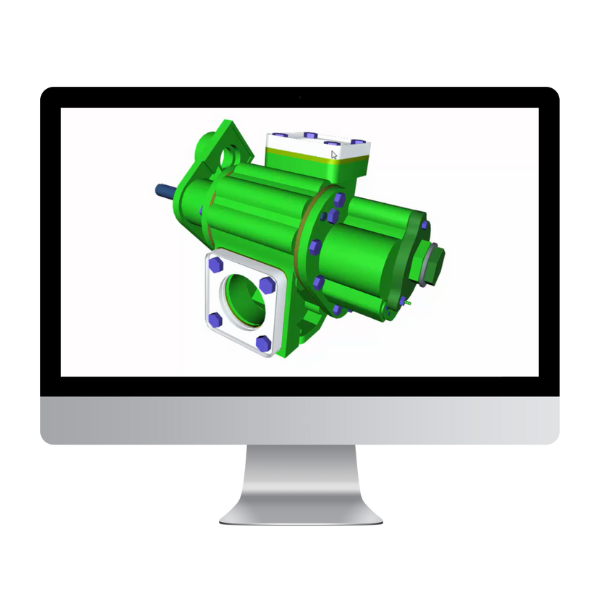
The creation and maintenance of traditional document databases cost companies a lot of time, resource and money.
We believe the key to effective product documentation for complex equipment is the reuse of existing 3D engineering and product data, for the creation of interactive 3D technical publications. Whether it's for maintenance, customer support, operational procedure's or training, better documentation can increase efficiencies and reduce down time - in turn delivering a strong return on investment (ROI) for your business.
RapidAuthor for Teamcenter® CMS
Teamcenter brings document processes into the PLM environment, synchronising them with product development processes and keeping content up-to-date with product changes.
Providing automated tools to reduce the time and cost to author and publish accurate, high-quality documentation tailored by market, language, or product configuration.
Cortona3D RapidAuthor
Cortona3D RapidAuthor is a powerful cost-effective authoring suite that gives the flexibility to produce all support documentation such as interactive Parts Catalogs, Maintenance Manuals, Training Materials and Work Instructions as 2D or 3D interactive visualisations utilising your existing CAD data.
Oxygen XML Editor
Oxygen XML Editor provides a comprehensive suite of XML authoring and development tools. It is designed to accommodate a large number of users, ranging from beginners to XML experts and is available on multiple platforms, as well as all major operating systems.
Technical Content Outsourcing
If the creation and maintenance of your technical content is proving too time consuming and resource heavy, then why not speak to CAD-IT about our technical content outsourcing services. Utilise our team of technical authors to produce your technical documentation, with the ability to scale up or down as demand requires.
Parts Catalogues
Maintenance Manuals
Training Manuals
Work Instruction
Operations Manuals
Technical Content Resources:
CAD-IT & INEOS Automotive
CAD-IT are key service partner for INEOS Automotive. Helping INEOS Automotive in their #Grenadier4x4 project to eliminate traditional problems associated with management of the service business, transforming service into a streamlined operation.
We provide an integrated end-to-end SLM solution and supporting services for INEOS Automotive, where our solutions are integrated into Teamcenter and ERP. The SBOM (Service Bill of Materials) is the heart of the solution, ensuring data efficiency, consistency, and accuracy. Connected solutions and processes bring richer, fully interactive, 3D content and provide a future gateway to Augmented Reality.
Request a free demonstration
We offer free no obligation demonstrations of all the solutions you see here. Simply follow the link to arrange a demonstration with one of our knowledgeable and helpful team members.
Proud to be working with
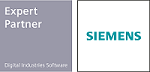
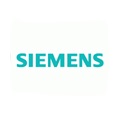
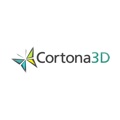
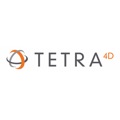
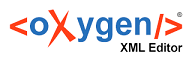